Carbon Footprint
Global warming potential (GWP), commonly known as a ‘carbon footprint’, measures the potential global warming impact of a process in CO2 equivalents of greenhouse gases between a defined start and end point. Different emissions can have a lesser or greater global warming impact so, for convenience, they are measured and then converted into ‘CO2 equivalents’ of greenhouse gases. For instance, one tonne of methane has the equivalent global warming impact of twenty five tonnes of carbon dioxide.
In the case of NatureFlex™, a complete LCA has been carried out from ‘Cradle to Gate’; this has allowed us to measure and understand the impacts of all our raw materials, through the whole of our manufacturing process until the finished slit reel of film is ready to leave our site. This work has been carried out by Sphera.
Significant improvements have been made to the raw materials we employ and to our manufacturing process, since we started monitoring our process using LCA in 2006. The most recent LCA was carried out in 2021 and shows that the carbon footprint has reduced by 35% since 2006. Historical data showed that already by 2006 the carbon footprint had reduced by 57% from the 1990’s. Looking forwards, we are predicting a further reduction of 40% by 2027 based on future investments in our process.
It is increasingly common for companies to seek to compare the carbon footprints of different materials, but great care must be taken to ensure that the comparisons are made only between materials with similar functional properties and using the same LCA methodologies and start and end points.
The graph shown below shows the carbon footprint values (kg CO2eq / kg) of various conventional plastic films (polyethylene, polypropylene, polyester and polyamide) together with the current carbon footprint of coated NatureFlex NK film. Also shown on the graph is a predicted carbon footprint for coated NatureFlex in 2027, following planned investments in the manufacturing process.
Whilst polyethylene film has the lowest carbon footprint, the properties of polyethylene are very different to NatureFlex and so NatureFlex is not a suitable alternative for polyethylene. NatureFlex is more similar to polypropylene, but in terms of density, mechanical properties, printability and heat resistance, polyester is the closest comparative film. NatureFlex is also a good alternative film for polyamide as NatureFlex has a very good oxygen barrier and has a similar stiffness.
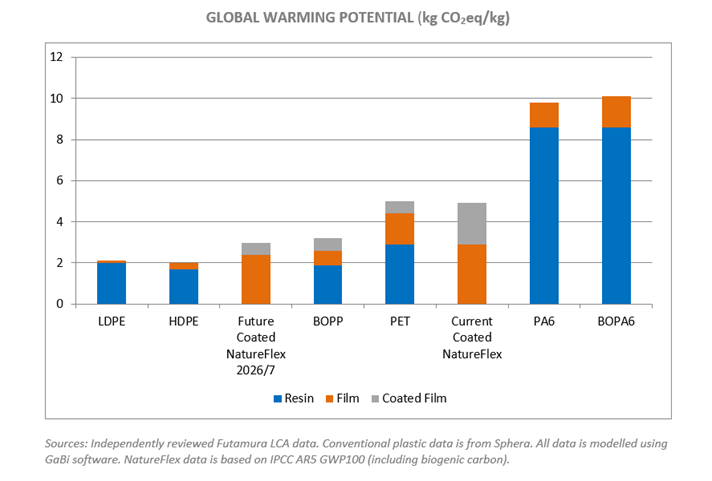